1.3.1 Technological transformation of water-based inks Through nearly 10 years to 15 years of technical improvements, the ink-and-water system has successfully solved most of the original difficulties, such as difficulty in use, ink storage, substrate limitations, and corona treatment and With surface tension and other issues, the new generation of ink and ink has changed its initial disadvantage as an advantage, and has gradually grown and matured.
Ink performance
1) Ink and ink have environmental and safety advantages. In many paper products, ink printing can be designed as low VOCs or zero V0Cs;
2) The ink has the advantages of stability and low flammability. The ink has a better viscosity stability due to the low volatility of water;
3) The new generation of water-based products is easier to clean than the solvent system. The use of soapy water or weakly alkaline lotion to scrub can complete the entire cleaning of the printing press parts, thereby improving the production efficiency.
The ink-and-wash manufacturers have overcome most of the difficulties that existed previously in the ink-and-wash system and are actively working to resolve the existing difficulties.
2. Insufficient application of ink technology
1) Drying time is still the most important issue in ink applications. Unless the press is equipped with enough drying equipment, the printing speed will be affected. This is also the most important factor affecting the speed of the process of replacing ink ink with solvent ink.
2) Because the ink is soluble in the alkaline solution, the use of the ink in a highly magnetic environment is limited;
3) The application of ink on frozen food packaging still does not have the solvent ink resistance, although the distance is rapidly shortened.
1.3.2 Technical Problems of Water Based Ink
When the quick-drying agent ink is used, the ink used by the ink manufacturer may be different or the machine speed may be too fast, which may cause the ink drying speed to be slower. Accelerating the drying agent can adjust the ink drying speed to the speed requirement of the printing press and increase the production efficiency. The use ratio is 2 to 3%. Slow drying agent It can inhibit and slow down the drying speed of ink, play a role in moisturizing, prevent the ink from drying on plates or anilox rollers, and reduce the occurrence of printing failures such as blocking and stencil printing. The use ratio is 1 to 2%. between.
Water-based inks used in the scope of the previous introduction of water-based ink structure and type, then we talk about some of the important factors that affect the quality of water-based ink printing. In paper pulp printing, the transfer of ink and ink is controlled by the anilox roller. For this reason, the anilox roller must be selected according to the requirements of the product. The number of lines of the anilox roller is approximately four times that of the printed line. In order to get better print clarity and resolution.
Fineness refers to the size of the toner particles in the ink. It is completed in the process of producing ink color paste. It is a key quality indicator. Whether or not the color paste production process is scientific and meticulous plays an absolute role in the quality of the ink. It is best to add dispersants and wetting agents during the production of pastes. The fineness of the general ink is required to be between 10 and 25 μm. Fine or too large will affect the ink flowability and rheological properties.
Viscosity refers to the thickness of ink and is an indicator of the flow of ink. The viscosity is too large to cause poor fluidity and slow drying; the low viscosity ink has good fluidity, fast drying, thin ink layers, and low ink consumption. Normal general ink viscosity is 50-65/25°C (coating 4# cups), high-grade ink viscosity is controlled at 25-35/25°C (coating 4# cups). If the viscosity of the ink is low, the toner content requirement is higher; otherwise, the toner content is low. Since the viscosity directly affects the transferability of the ink and the quality of the printed matter, the control of the viscosity of the ink is very important for this purpose. In the printing process, if the viscosity is too low, the color will be light, and the high viscosity will cause the phenomenon of dirty plate, stencil, etc. Therefore, if the transfer agent is difficult to control, the transfer agent can be added to improve the transfer effect and increase the vividness and three-dimensionality.
1.3.3 Problems with Aqueous Ink Additives
Auxiliaries commonly used in water-based inks. There are pH stabilizers, defoamers, fast drying agents and slow drying agents.
pH stabilizer
The pH stabilizer is mainly used to adjust the pH value of the ink and the pH value of the ink. Through the ink manufacturers, it is often mentioned that the ink product is promoted to the printing enterprise. The low pH value easily causes the ink to agglomerate, and the viscosity is high when the pH is high. Is relatively low. Generally, during the printing process, the pH value of the ink should be detected. When the pH is lower than 8, an appropriate amount of pH stabilizer should be added so that the ink can maintain a good printing state. The pH value of the European national ink is based on neutrality. When the pH value is adjusted to 8.5, the fluidity and glossiness are in the best state. However, in the printing process (one hour), the viscosity of the ink is evaporated due to the evaporation of the amine solvent. It will rapidly increase, the gloss will decline, and the fluidity will deteriorate. As a result, there will be a large number of unqualified products, such as adjusting the pH value, adding amine solvent, and continuously testing (within one hour) during the printing process. ), a little carelessness, waste products will appear, and the entire workshop is full of unpleasant odors, such products are considered poor in printability, such as the pH value of the ink between 7-8, ink and wash The best stability, the user can add pure water as a solvent to reduce the viscosity, so as not to increase the cost, but also make the ink resin taste reduced.
Defoamer
Defoamer ink viscosity is too high, the pH is low, the printing speed is faster and printing technicians add too much water, are prone to air bubbles. When the bubbles are relatively large, there will be phenomena such as whitening of the printed matter and less ink, which will seriously affect the printing quality. It is generally recommended to use a mixture of foam suppressor and surface defoamer in the ink to solve the blistering of the ink. The use ratio is 1 to 2%.
3. Fast drying agent
When the quick-drying agent ink is used, the ink used by the ink manufacturer may be different or the machine speed may be too fast, which may cause the ink drying speed to be slower. Accelerating the drying agent can adjust the ink drying speed to the speed requirement of the printing press and increase the production efficiency. The use ratio is 2 to 3%.
4. Slow drying agent
Slow drying agent It can inhibit and slow down the drying speed of ink, play a role in moisturizing, prevent the ink from drying on plates or anilox rollers, and reduce the occurrence of printing failures such as blocking and stencil printing. The use ratio is 1 to 2%. between.
1.3.4 Usage of Water-based Ink
1. Can not mix ink with solvent ink. In the use of appropriate addition of water, you really need to adjust the viscosity or drying speed, the appropriate amount of additives such as alcohols or esters.
2. Stir before use and then pour it into the ink tank. Adjust the viscosity with water and use it. Unused containers should be covered and the ink should not be allowed to evaporate in nature.
3. Before use, check the technical indicators, especially whether the hue meets their own requirements. If the hue deviation is large, please notify the ink manufacturers to properly deploy, so as to avoid the dispute caused by the hue error.
4. In the printing process, due to the volatilization of water, the original viscosity and pH value of the ink will be affected, and the viscosity and pH value need to be constantly detected. If necessary, pure tap water or pH stabilizer should be properly added.
5. The ink remaining on the printing equipment after printing is rinsed with clean water. The ink on the printing roller is preferably cleaned with a cleaning agent for the next printing service.
1.3.5 Getting out of water-based inks Misunderstandings Not all users of water-based inks understand the principle of viscosity, and many people have the misconception that the viscosity of a water-based ink is a good one. Can add a lot of water, printing more cardboard boxes, reduce costs and increase efficiency. In fact, we do not blindly purchase high-grade ink based on the performance of production equipment. We believe that with high-grade ink, we can print good-quality prints. This is very impractical and unscientific.
The simplest test for high-grade ink is whether there is discoloration, but ink that does not lose color is high-end, or that high-end ink is not lost, and is not particularly accurate. Because the problem of color loss is still a problem in the world so far, there is no ink factory that can make ink that does not lose color. If the ink is not discolored, the only way to do this is to use offset ink printing, either over a layer of varnish or over a layer of PVC.
The print effect of a printed matter is affected by many factors, such as printing presses, ink, paperboard, technical operators, and climate change. However, once end-users report problems with the carton, the carton factory will often look for ink and ink manufacturers for the first time. In fact, this type of problem should be looked for in many ways. It is indeed the quality problem of the ink itself that should adopt economic measures to punish the ink manufacturer.
At present, the price of ink is relatively low, and the profit margin is relatively small. Carton printers, however, have relatively tight cost control and are desperately trying to lower the price of ink and ink. In general, ink-jet printers are in a poor position to cope with reducing costs. There is no time and sufficient funds to develop products and improve product quality to better serve carton factories. In fact, the cost of paper is the key point. Most of the carton plant's production costs are on paper or cardboard. The cost of ink in a carton is less than 0.01%, and spending so much time and energy to deal with ink prices is not worth it. In addition, some ink-jet factories sell computer-grade toners to carton factories in order to sell service brands. The carton factory believes that it is a treasure that actually increases the production costs of carton factories.
Because it is not a universal color palette, it is rarely purchased in other industries except the high-consumption automotive paint baking machine configuration computerized color mixing machine. As a low-value consumables, the carton industry must be equipped with a computerized color mixing machine to increase expenses. You can talk about seeing people, it is worth considering.
1.4 Production Status of Water-based Ink
In recent years, flexographic printing has developed rapidly around the world and is considered to be “the best and most promising printing method on the planet†in developed countries in Europe and America. In the United States, 95% of flexographic prints and 80% of gravure prints use ink. Flexographic printing is still in its infancy in China and currently accounts for only about 3% of the printing industry. However, with the increasing popularity of environmentally-friendly packaging, many tobacco companies, wineries, pharmaceutical companies, cosmetics factories, and children's toy companies are all planning to use flexible printing products. The proportion of flexo printing in the printing industry will gradually increase. Is the field of packaging and printing. In the flexo package printing, the vast majority of domestic and foreign water-based ink printing. From 1995 to the end of 1998, China has introduced more than 130 modular flexo production lines in more than 20 provinces and cities in the past few years. There are currently nearly 200 narrow-width flexographic printing production lines in China. The number of 30 or so units is increasing every year, and there are also many imported high-end three-color and four-color water-based ink printing and slotting machines for color printing of corrugated paper.
China has an average of more than 1,000 carton factories per province. If we use 10% water-based ink to print high-grade cartons, each household ink is calculated at 10 tons. Each province needs about 1,000 tons of water-based ink each year. The volume of flexographic printing in the printing sector will reach 15% by 2010, and it will require more than 150,000 tons of water-based ink annually. This does not include inks used in other printing and packaging products for flexo and gravure printing (currently, 100% of domestic flexographic printing uses water-based ink, and 80% of gravure printing uses water-based ink). It is imperative to vigorously develop, develop and produce high-grade water-based inks. The product can be widely used in gold and silver cardboard, coated paper, slat paper, plastic film, corrugated paper, self-adhesive paper, carton, paper packaging, books and periodicals. Printed flexographic and gravure printing areas such as magazines.
1.5 advantages and disadvantages of water-based ink
1.5.1 Huge "green" advantage
Due to the absence of volatile organic solvents, water-based inks greatly reduce the emission of organic volatiles (VOCs, the same below), thereby reducing air pollution, improving the environment for printing operators, and contributing to the health of employees. It can completely eliminate certain toxic and harmful substances in solvent-based inks, eliminate the harm to human body and the pollution of packaged goods, and improve the overall environmental quality. It is especially suitable for tobacco, wine, food, beverages, medicines, children's toys and other health Conditions require strict packaging and printing products. In addition, it can not only reduce the risk of fire and hidden dangers caused by static electricity and flammable solvents, but also reduce the toxicity of printed surface residues, and it is convenient for cleaning printing equipment.
1.5.2 Problems with aqueous ink
Whether it is imported water-based inks or domestic water-based inks, there are currently disadvantages such as non-alkaline resistance, non-anti-ethanol and water resistance, slow drying, poor glossiness, and easy paper shrinkage. To achieve alkali resistance, ethanol resistance, water resistance, and gloss enhancement, only flexographic UV inks are used. This not only increases the cost of printing, but also increases
Rest assured material: bite and snake belly using food grade environmental protection silicone material, guaranteed. The new water stop system uses Zero Resistance speed water stop system, single ball shaft, effectively prevent sand jammed stop valve, bead valve has been in the center of gravity balance position, effectively solve valve failure and other problems.
Corrugated Silicone Hose quality silicone corrugated hose, from any angle for 180 degrees fold will not occur air blocking, even if the high speed forward, tumbling, and cope with the impact of the waves, can also be relaxed.
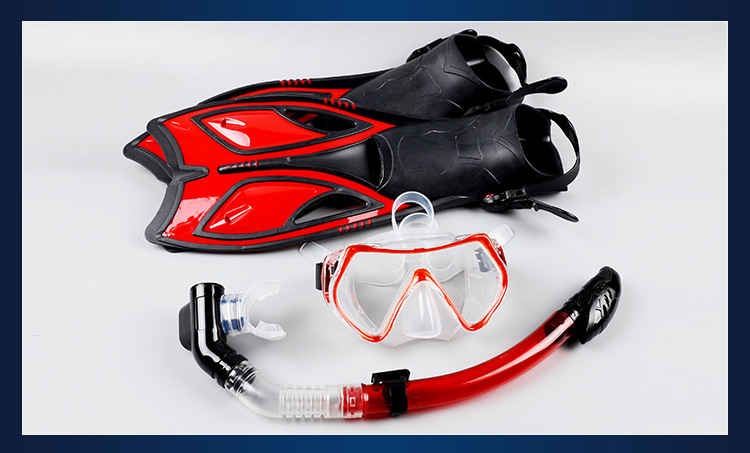
Snorkeling Wetsuit,Diving Suit,Diving Wetsuit,Surfing Suit
Yangzhou Sainuo Star Sports Products Co., Ltd. , http://www.cnsportsgoods.com